- June 14, 2023
- Posted by: David Marshall
- Category: Innovation, Management, Manufacturing, Productivity
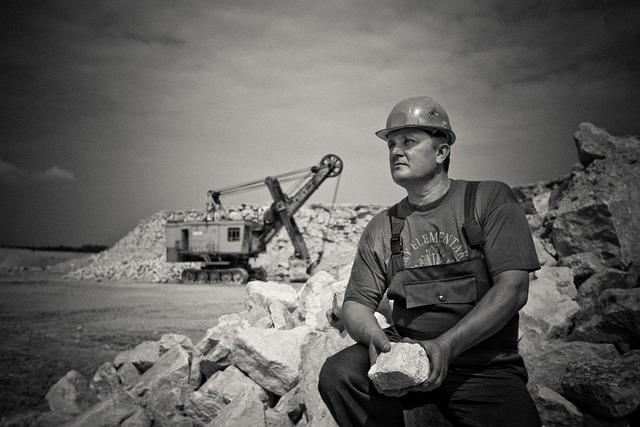
As much as I hate to say it, the key to increased productivity really is “work smarter, not harder.”
But it’s more than just finding little tricks and hacks that help people do their job much faster, or having people start working a little faster than they were before.
If you really want to increase productivity in a manufacturing setting, you need a pretty active industrial engineering group who work with your people to understand what would make their job easier.
For example, we set ergonomic limits that no one should pick up more than 20 pounds of weight. If you look at a 6-inch piece of steel pipe, a 6-foot length weighs 200 pounds, which means you would need at least two people to handle that. Or you can install equipment that will help you lift it, move it, and position it.
The good thing about that equipment is that it doesn’t have injuries, show up hungover, or call in sick. It will keep working and working. So we worked with our industrial engineers to create and install the equipment that did the heavy work while we set productivity and ergonomic goals and looked for ways to be able to do that without flogging our employees.
When Should You Make Changes to Processes?
You should have consistent goals you set for productivity, even if it’s incremental changes. Let’s say you’re at 95% efficiency, so how do you get to 100%?
That may mean you have to analyze the methods used in that workstation or production line to find the bottlenecks. Once you’ve identified them, the next step is to figure out the solutions to that. What’s causing them? What’s the best solution? Do you need a different machine, a different operator, or a whole new set of procedures?
That should be an ongoing process, just like you’re looking at a person’s performance on an ongoing basis. You should also be looking at your machines’ and your systems’ performance in the same way.
That means, doing this more than once a year in an annual review. If you’re not reviewing things on a regular basis, there’s a good chance you’re going to miss a problem and let it go on for an entire year before you spot it again.
Imagine finding out there’s a system issue that has been going on for 51 weeks.
If you’re reviewing your productivity on a daily basis, you should be able to spot patterns and problems after a few days. This means consistent monitoring and watching your dashboards for inefficiencies. That way if something goes below a certain level, you have to find out why. And if they go above a certain level, you need to know why.
The former could mean someone is sick, a machine is broken, or there’s a problem further up the line. The latter could mean you’ve made improvements in your area, but you haven’t adjusted your standards. So if you’re running 5%, 10%, or even 150% above your standards for a couple months, you need to adjust your standard. By making improvements in your system, you’re going to see the effects travel down the line, so you need to adjust for those accordingly.
So yes, increasing productivity means working smarter, but it doesn’t always fall on the individual operators to make better decisions. An equal amount of the work should fall on your maintenance team and your industrial engineering team. They’re the ones who should be looking for the smarter ways to work and to find improvements in your company.
If you don’t have a team, consider either hiring some or bring in one or two as consultants to troubleshoot your processes and find new places to improve. Implement those changes and monitor the improvements so you can measure the ROI of their efforts. As you make more money, you can hire them again and again to continue to find more improvements until you reach the point that you have maximized your gains and reached peak performance.
Photo credit: Pexels (Pixabay, Creative Commons 0)