- May 24, 2023
- Posted by: David Marshall
- Category: Manufacturing, Safety
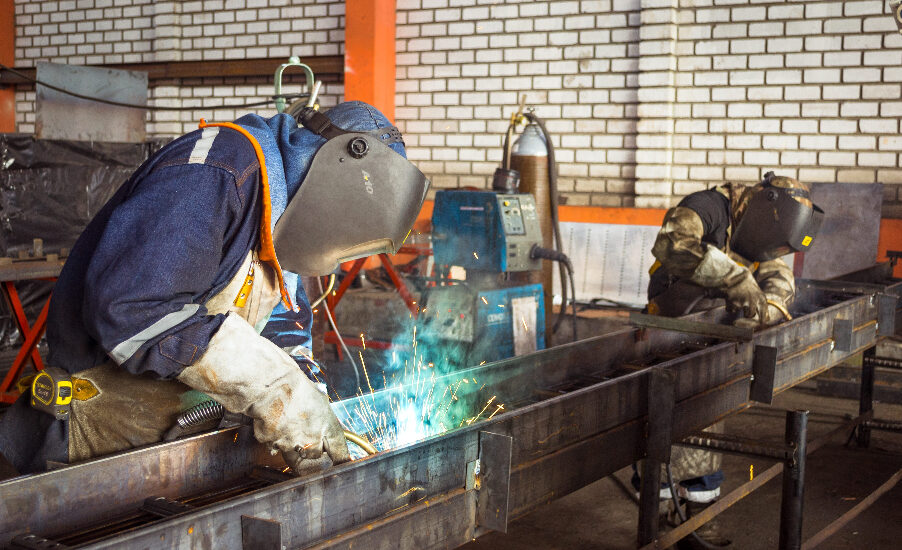
When it comes to deciding who’s responsible for an individual’s safety, there’s only one right answer.
EVERYONE
Anyone near them. Anyone on the other side of the room or the other side of the building. Anyone who happens to be walking by. It’s no one person’s job, it’s everyone’s job.
Everyone is responsible for everyone else. Or, to put it another way, yes, you are your brother’s (or sister’s) keeper.
When it comes to safety, an accident is often the result of a chain reaction of events. It’s not just one person making one bad decision, although that’s often the case. But more often, it’s a string of events, sort of like an aircraft going down is not just because of one single event.
Think of it this way: let’s say someone is walking across the factory floor, and they slip on a puddle of water.
Is the slip the accident? Do we blame the person for not avoiding the puddle?
No, the more important question is to ask why the puddle was there in the first place. Did someone spill their water bottle? Why didn’t they clean it up? Was a machine leaking? Why didn’t maintenance fix it? Did they know about it? Then why didn’t the operator tell maintenance about it? Is there a leak in the roof? How long has it been there?
I once had a crew of seven people putting a product together, in an assembly line fashion. The first person in the line noticed that one of the parts he was working with was poorly made and had a defect. But he installed it anyway.
The second person in line also saw it but said nothing. He just passed it on after doing his own part. And the third person saw it and said nothing. And the fourth, the fifth, the sixth, and the seventh.
The person who saw it and said something? The quality control checker who was getting the products ready for delivery.
All seven people let that defective item go through. They did their work, processed their part, got paid for it, and we had to reject the final product — which was just teeming with all the overhead and salary costs — and discard it completely.
Needless to say, all seven people were fired, because no one took responsibility for saying, “Hey, this is wrong. We need to stop the line.”
I could have accepted that. At least we wouldn’t have wasted all that time and money. We could have replaced the defective part and not the entire assembly. Instead, everyone assumed someone else would speak up, or that it wasn’t their job.
Do you see how it works?
You can’t wait for someone else to point out an unsafe practice, you have to do it. Because it’s everyone’s job.
By pointing out someone else’s unsafe practice, you’re not getting them in trouble, you’re helping yourself because you could be next in the chain.
That means when we provided safety training for our employees, we made sure they knew they were policing themselves and each other. They were taking responsibility for themselves.
Every now and again, we’d get some bonehead who decided he would do what he wanted to do, regardless of the training and the rules we had in place. We needed someone to point that out fast and be willing to speak up because that bonehead could cause a chain reaction that could get someone killed.
So they didn’t just go to the manager and mention it. They didn’t fill out a complaint card or send an anonymous email. They had an absolute right to bring the facility to a standstill to fix a safety issue. And they did.
We had an oven that had a tendency to overheat. We were curing PVC in that oven, and of course, we wanted to avoid a fire. We had one guy who had been watching this oven operate for a while, and he saw that it overheated on a regular basis. If we ran it too long, it was going to completely overheat and completely combust.
The associate quickly pulled the plug and said this was a serious problem. So the whole operation came to a standstill. All PVC curing stopped, and that put us immediately behind schedule.
It was worth it.
Upon further investigation, we found that the exhaust fans were not operating at maximum capacity. They weren’t removing all of the heat, which meant it was building up inside the oven, which was about to cause a fire.
This person did absolutely the right thing at the right moment. The fix was just a matter of replacing the fans and the insulation within the flue, which took about four days to fix.
We were shut down for four days, but it was far better than the aftereffects and fallout that would have resulted after a fire.
We would have had serious damage worth tens of thousands of dollars and would have had to rebuild and replace, which would have been tens of thousands more dollars. And we would have been shut down a whole lot longer than four days.
While some people would have told the associate to ignore the problem and do his best to bleed off the heat, we created a system where safety was our number one non-negotiable, and that took precedence over profits and productivity.
After all, there’s no point in maximizing profits over safety when you have to pay all those profits out in an injury or wrongful death lawsuit.
I’ve been a manufacturing executive, as well as a sales and marketing professional, for a few decades. Now I help companies turn around their own business, including pivoting within their industry. If you would like more information, please visit my website and connect with me on Twitter, Facebook, or LinkedIn.
Photo credit: PXFuel (Creative Commons 0)