- November 25, 2020
- Posted by: David Marshall
- Category: Digital Transformation, Manufacturing
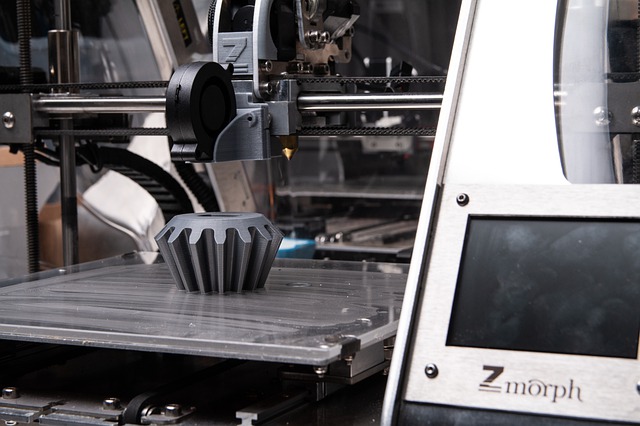
I recently saw an article that called additive manufacturing the next industrial revolution, and I thought they couldn’t be more right.
Of course, we all know about the original Industrial Revolution and how it has shaped society today, including working hours, salaries, trade unions, and even the idea of the weekend. Robotics and digital manufacturing have changed the face of manufacturing, bringing it to what is being called Manufacturing 4.0.
And now additive manufacturing will be a new industrial revolution, combining what’s best about manufacturing 4.0 and getting rid of the inefficiencies of older manufacturing methods: We could see parts of the manufacturing industry turned on its head over the next 20 years.
Additive manufacturing is also known as 3D printing, but we call it additive manufacturing to differentiate it from the home hobbyists who use desktop printers. These are large-scale printers that are printing in steel, titanium, and some plastics. (Don’t scoff at the home hobbyists, though! Those kids are going to become your high-skilled labor force in about ten years.)
Here are a few of the ways that additive manufacturing is going to change modern manufacturing as we know it. If you get on the train right now, you can become the leader in your industry or region before your competitors.
- Traditional tool-and-die, molten steel manufacturers will shrink. That’s not to say they’ll go away completely, but how many local tool-and-die shops are struggling? What will happen when their customers start doing industrial 3D printing? Tool-and-die makers would be smart to embrace 3D printing first.
- Orders of tens of thousands of small parts will start to disappear. Manufacturers who only need a few small parts at once will stop buying a 10-year inventory of tiny parts. They’ll start printing their own small parts, or they’ll buy them from a 3D printer who will happily sell them 50 pieces a week.
- Distributors will (or should) become 3D printers. If you’ve got a distribution company that’s buying tens of thousands of parts from China in order to ship them to U.S. customers, why not become an additive manufacturer yourself? Print the parts and sell them on demand instead.
- Reduces the need for warehouse space. What if you could just print your parts on demand rather than buying and storing months’ worth of inventory? What if you could reduce your storage space requirements by 25%? What could that do to your overall footprint? Hell, with that much saved space, you could add a few more printers. . . (See how this works?)
- Manufacturing facilities will get smaller. When we upgraded our Duoline facility, we actually tore down the old facility and built a newer, smaller one. A company that wanted to do basic additive manufacturing could put 2 – 5 small industrial 3D printers in something the size of a small house. No more 20,000 sq. ft. buildings and giant iron machines, just a few printers, desktop computers, and workstations.
- Smaller, highly-paid workforce. Digital manufacturing already calls for a high-skilled workforce to operate it, but now you’ll be looking for people who can easily make 3D designs and operate the machines. And you’ll only need a few employees, not dozens or hundreds.
- This will disrupt overseas manufacturing. Instead of ordering parts from overseas manufacturers two months before you need them, you can make them in your own operation a few days before the customer needs them.
- This will disrupt shipping and logistics. Think of all the parts that are shipped to you that you could make in-house, or at least buy locally. How many shipments would you reduce if you made those small parts? Now multiply that by every manufacturer and distributor in the country, and you’ll get an idea of the impact. This won’t eliminate shipping and logistics, but it will take a bite out of their OEM loads.
- More entrepreneurial manufacturers. Given the relatively low cost of an industrial 3D printer (between $20,000 – $100,000), we may see more manufacturing startups in the coming years. Like I said before, all it takes is a single industrial printer and a small space, and you’re in business. You could start a small manufacturing company in a 10′ x 20′ outbuilding, a bay in an industrial park, or even a business incubator.
I’ve been a manufacturing executive, as well as a sales and marketing professional, for a few decades. Now I help companies turn around their own business, including embracing additive manufacturing and digital manufacturing. If you would like more information, please visit my website and connect with me on Twitter, Facebook, or LinkedIn.
Photo credit: ZMorph3D (Pixabay, Creative Commons 0)