- April 18, 2020
- Posted by: David Marshall
- Category: Digital Transformation, Manufacturing
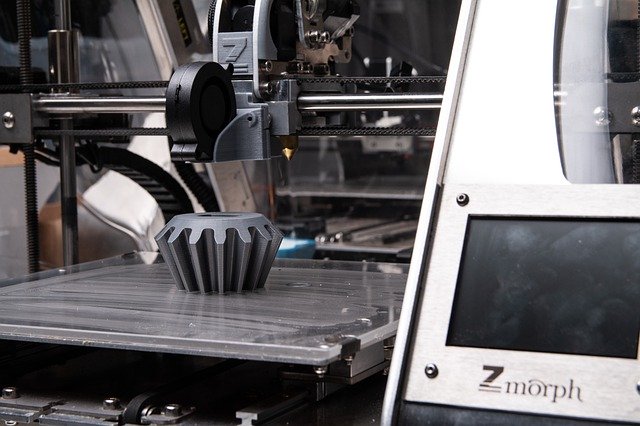
One of the most interesting industrial developments during this COVID-19 pandemic is how several different companies have begun 3D printing ventilator masks, valves, and face shields.
We first started hearing about companies stepping up and helping with the pandemic fight when Italian company Innova began printing replacement valves for ventilators after the ventilator manufacturer said they would take a few weeks to manufacture and would cost $11,0000 each. The replacement valves only cost $1 to make and were done in a day. (Of course, the original manufacturer may take legal action, which is somehow not surprising.)
After Innova began printing the 3D valves for their local hospital in Brescia, other 3D printing companies and home hobbyists began printing different components to make N95 ventilation masks and face shields, even as other companies, sewing groups, and individuals began making surgical masks for hospital staff and civilians. They’re especially turning to this option after regular suppliers in the private sector and the federal government have failed to deliver ordered items.
I’ve thought that this was a great testament to the commitment and ingenuity of the people in this country: Being able to come together for a single purpose, whether it’s a single event in a single place or the crisis is spread out throughout the entire country.
I’ve especially appreciated how hundreds of manufacturers have been able to bring their resources to bear on just a few products and make them to match the specs that the first responders need in order to function and survive.
Even now, small manufacturers, maker spaces, and home hobbyists are 3D printing face shields and ventilator masks, while sewing groups and individual “sewists”* are producing cloth face masks for people to wear in public.
* I learned that people who sew prefer the term “sewist” to “sewer,” at least on the Internet sewing sites.
We’ve already seen this many-for-one model work in a number of different industries, such as automotive manufacturing. The automotive manufacturer is not actually a manufacturer of cars, they’re an assembler of parts that are made by other manufacturers — axles, frames, doors, windshields, shock absorbers and struts, and so on. Each piece is made to precisely fit together in a single design for a single purpose.
And the way the production is spread out among hundreds, if not thousands, of home hobbyists and small businesses who can only produce a small number of units per day is also impressive. They’re sharing the load, each producing a small part to make up a greater whole.
This has been a common practice for Nucor Steel, which builds micro steel mills in different parts of the country to serve nearby customers. Years ago, Nucor found this to be a much more efficient practice, rather than building one or two gigantic steel mills and shipping steel all over the country.
In the case of the pandemic, many of these producers are fundamentally helping others without the expectation of being paid. That may not be the case for the companies making $11,000 parts for ventilators, but many of the 3D printing companies and individuals are certainly doing that.
It has a lot to do with technology
This kind of approach would not necessarily have been possible 15 – 20 years ago. But now, thanks to things like crowdsourcing and open source sharing of files and schematics, people can upload digital plans for a particular 3D-printable item, make comments and adjustments, upload that plan, until the thing is perfected. From there, people can download that schematic to their printer and reproduce as many of those items as they want.
This is the same kind of thinking that goes into digital twinning, the idea that you could build a digital manufacturing system and then reproduce it without error or deviation in another part of the world.
A digital twin lets you see data and information from a manufacturing operation in one place and then comparing it to another manufacturing setup somewhere else. This can be done with manufacturing operations around the world, not just the same building.
The efficiency of digital twinning means you can transfer the settings and information to different locations. This saves you from having an expert in the company who flies all over the country or the world setting up machines and making adjustments. Instead, you can create a digital twin of your system and then share it with your other factories.
Or 3D printing enthusiasts and sewists can share digital files with each other around the world in order to save it.
I’ve been a manufacturing executive, as well as a sales and marketing professional, for a few decades. Now I help companies turn around their own business. If you would like more information, please visit my website and connect with me on Twitter, Facebook, or LinkedIn.
Photo credit: ZMorph3D (Pixabay.com, Creative Commons 0)