- February 1, 2017
- Posted by: David Marshall
- Category: Business, Manufacturing, Productivity
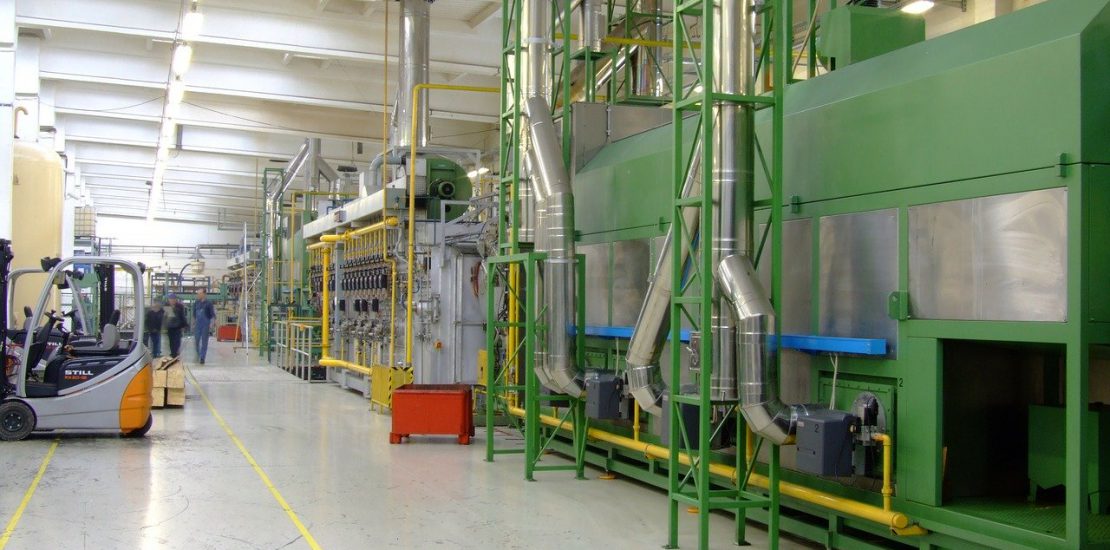
In a manufacturing operation that measures everything, it’s especially important to measure the operational time of your plant and its associates, to ensure they’re being as productive as possible. Some people call this measurement “time keeping,” but that term can also be confused with associates clocking in and out in the course of a normal work day.
Clocking in and out is one element of timekeeping. But we want to know whether they are active and doing something that adds value during their clocked-in time. So we want to think of timekeeping as when our associates are actually producing goods, and not just how much time they spend in the building.
But timekeeping isn’t the only critical measure to consider in a plant’s productivity, no more than only measuring the number of units created in a single week. Instead, we need to measure different aspects of a plant’s work on a minute-by-minute basis, including parts produced, associate productivity, and so on.
This is all part of the plant workflow.
Plant workflow measurement examines everything, including the associate’s time, whether the equipment is up or down, the consumption of bulk materials on a minute by minute basis. All this information is fed from the central ERP system, which downloads the requirements for the facility to the plant workflow system. It eliminates paper and it directs the workforce as to what is required to be done. That way, the associates can self-manage their own performance.
That all starts with establishing standards on every item you create or assemble. Once these standards have been established through a bill of material, a plant workflow system will show you hour-by-hour whether the associates or group of associates are being efficient at what they do.
You can also spot problem areas and opportunities for improvement based on the department, associate, and even the machine they used.
If a piece of equipment goes down for some reason, you can track how long, how frequently, and why the equipment is down. Your goal is to always ensure the equipment is up and running, so if you can understand why it’s down, you can find a temporary and then a permanent fix to ensure it doesn’t go down for that particular reason again.
If your equipment is hooked up to a programmable logic controller (PLC), and a plant workflow measurement system, the PLC will monitor the equipment and send an alert either by email or even a big red light saying something is not right with that piece of equipment. The machine may not have stopped, but something is not right, which means maintenance can give it immediate attention and prevent any actual downtime. This saves money, because it keeps the machine producing products, and keeps the associate productive as well.
These are just a few examples of how a plant workflow measurement system can greatly benefit a manufacturing operation. At my manufacturing plant we measured everything. In this way, we could operate at peak efficiency, which not only helped us find areas of savings, but helped us increase revenues and profitability overall.
I’ve been a manufacturing executive, as well as a sales and marketing professional, for a few decades. Now I help companies turn around their own business. If you would like more information, please visit my website and connect with me on Twitter or LinkedIn.
Photo credit: Marcin049 (Pixabay.com, Creative Commons 0)