- September 13, 2023
- Posted by: David Marshall
- Category: Innovation, Leadership
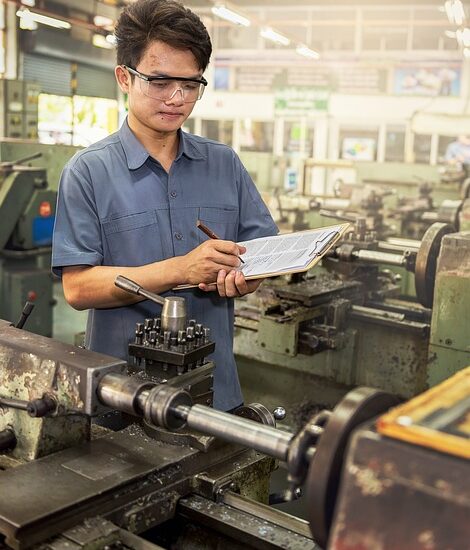
Manufacturing CEOs and COOs often deal with company-wide changes and projects that can affect how the entire business operates. One question we often dealt with at Robroy was whether to enlist the services of external experts during these challenges.
The decision to bring in outside expertise can be a game-changer. There were times, like when we needed to innovate new products or methods, we would bring in an outside industrial engineer to oversee the changes. And there were other times, like when we added warehouse management software or switched out our ERP software, when we relied on internal champions.
The Role of Internal Champions
The presence of internal champions is invaluable during major changes. These people are deeply ingrained within the company and have an innate understanding of its values, culture, and processes. They not only embrace the change, but they’ll rally the company around it.
In our case, our internal champions were instrumental in driving change from within. They bridged the gap between our existing practices — including any internal resistance among our associates — and the desired outcome. For manufacturers, this often involves aligning processes, technology, and people with the company’s overarching goals.
That can be a bit of a sticky wicket, so your champions also need buy-in from top leadership. Without it, there are no consequences for people who fail to engage, and thus, they’ll cock up the entire changeover so that it never functions at its fullest.
External Experts: A Wellspring of Specialized Knowledge
While the internal champions are the linchpin and leaders of the changes, external experts bring an added dimension to the fray. These specialists offer an outsider’s perspective and a wealth of expert knowledge. Their insights can be invaluable when dealing with complex software changes, innovating product changes, or optimizing different manufacturing processes.
External experts are great at teaching employees new software/process/manufacturing operations, understanding its intricacies and small tricks of the trade. They can speed up the learning process, which makes the transition much smoother and more efficient.
The Symbiotic Relationship
The relationship between the internal champions and external experts is where the real magic happens. The internal folks know the organization’s ins and outs, but the external experts offer a fresh perspective and know the latest methodologies and practices. They can avoid the pitfalls of insular thinking, such as “we’ve always done it this way.” The fact that they’re on the outside means they’re exposed to new methods and ideas in order to keep up with their field’s changes.
In manufacturing, it’s not a matter of which approach is better or choosing one over the other. Instead, you should strike a balance between these two pillars. Internal champions ensure the changes align with the company’s values; external experts have the technical know-how and a broader view of industry best practices.
Make Incremental Changes to Avoid Chaos
Manufacturers are at a threshold of making major changes to the industry. Whether you’re adopting a new ERP software solution or jumping on the additive manufacturing bandwagon, a word of caution is necessary.
Trying to change everything at once or changing for the sake of change will lead to chaos and disruption. This is where your external experts can help in structuring the changes. They can break down these transformations into manageable, incremental chunks. That not only reduces the risk of chaos, but it makes sure that the new changes align with your long-term objectives.
Dealing With the Human Element
In manufacturing, your people are the critical factor in change management. Don’t underestimate your associates’ concerns, fears, and resistance to change — they will not just fall in line because you said so. If you’re going to successfully implement a change, you need to provide employees with the necessary training, support, and motivation.
One effective strategy is encouraging employees to become experts in the new systems. This not only helps them protect their positions but also makes them a part of the organization’s growth. If you can identify the people who might otherwise be resistant to the change, appoint them as some of the co-leaders of the change. Offer them bonuses and recognition for undertaking the new role, and get them on your side immediately instead of battling with them down the road.
Take a Balanced Approach
Involving external experts in major undertakings or changes is not a simple yes-or-no proposition. It’s a matter of finding the right balance between internal champions and external expertise — think of it as a continuum, not a check box.
Your goal is to align change with your company’s culture, adopt incremental strategies, and address the human element in change management. So, if you need a combination of internal and external experts to make that happen, so be it.
The manufacturing industry’s success lies in using internal champions and external experts harmoniously. By embracing the strengths of each, you can navigate the ever-evolving landscape of manufacturing operations with confidence and resilience.
I’ve been a manufacturing executive, as well as a sales and marketing professional, for a few decades. Now I help companies turn around their own business, including pivoting within their industry. If you would like more information, please visit my website and connect with me on Twitter, Facebook, or LinkedIn.
Photo credit: Sasint (Pixabay, Creative Commons 0)