- July 28, 2021
- Posted by: David Marshall
- Category: Business, Management, Manufacturing
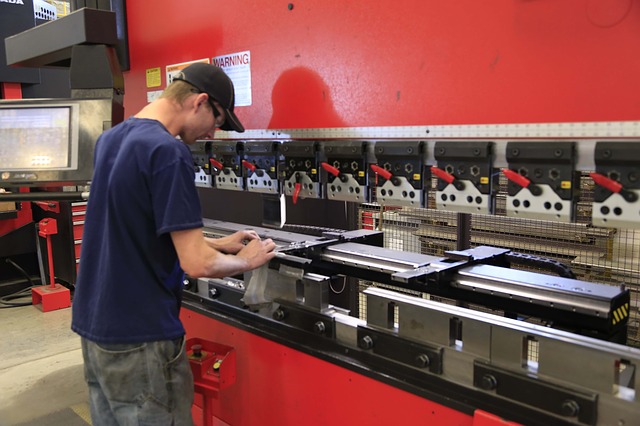
There are worker shortages right now in all kinds of industries, from the restaurant industry to office workers to manufacturing. There are a variety of causes, like the fact that we’re paying people more not to work than what they were being paid to work. Or that some people don’t want to return to the office and would rather work from home. Manufacturers are having their own issues with hiring people.
If I were facing a worker shortage like this right now, the first thing I would do is start by reducing shifts and getting rid of the dead weight, to begin with. A lot of times, the reason there’s a worker shortage is because some employees aren’t actually doing any work, and they’re collecting a paycheck. Getting rid of the deadweight can actually improve productivity.
When I first started managing Robroy, I cut our shifts back from three to two by firing people who were sleeping on the third shift and getting rid of people on all the shifts who weren’t pulling their weight at all. We cut back to two shifts and got more done than in three shifts with more people.
You can also cross-train your workforce. Make sure everyone can do at least one other function on the floor so you can move people from one place to another. This way, if you have a greater demand for one function one day, you can move someone over and fill a gap.
I would also raise prices on your products, at least temporarily. It will help slow the demand but still let you keep the same level of revenue. People who absolutely need your product will pay for it and you can serve them well, but the people who look for an alternative won’t stress your system.
And I know I keep beating this drum over and over, but I would also start measuring everyone’s results. If nothing else, this will help you identify problems that are leading to a lot of waste and returned products. If you could make everything right the first time, you wouldn’t need overtime and extra shifts to fix all the errors being created.
Another step is to upgrade to digital manufacturing whenever possible. If you can have computers and automated machines doing a lot of the work, you can reduce the number of people needed to complete a process.
We cut one factory from 140 to 20 employees by switching over to a digital manufacturing operation. This was a plant that often had a problem keeping associates, and I would lose 20 percent of my workforce any time we had a drug test. Once we revamped the entire plant, we brought the 20 best people back and produced four times as much as the old system.
If these aren’t on your strategic planning horizon already, they should be. Because if you’re not looking to improve your workforce and your equipment now, you’re ultimately going to fail. These are 2 – 5 year projects, not things you can implement in 90 days.
There are some quick-fix measures you can take, like signing bonuses and same-day pay, but these are all transitory. If you offered someone a $1,000 signing bonus or paid them the next day, there’s no guarantee they’ll show up a week later.
I’ve been a manufacturing executive, as well as a sales and marketing professional, for a few decades. Now I help companies turn around their own business, including pivoting within their industry. If you would like more information, please visit my website and connect with me on Twitter, Facebook, or LinkedIn.