- June 16, 2021
- Posted by: David Marshall
- Category: Management, Safety
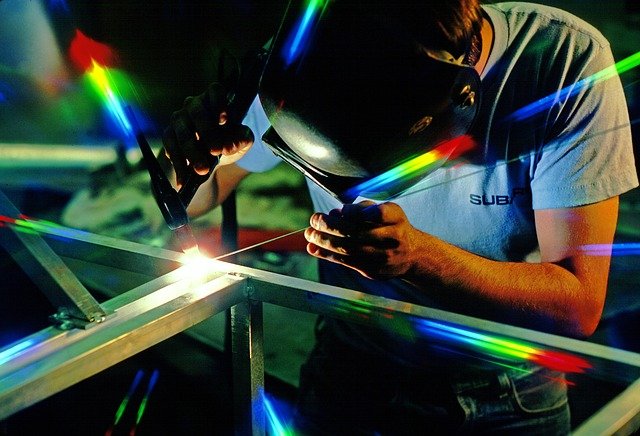
As a manufacturing manager, the worst words you can hear are “workplace injury.” Manufacturing is not necessarily a safe job, and people can get hurt just doing their work. Even with all the employee health and safety training, policies, and personal protective equipment, people can still get hurt on the job.
That creates a lot of hardship for the associate. For one thing, they’re in pain. They could be permanently disabled. In some rare instances, people die on the job. If the associate is lucky, they’re only off the job for a few days. The injury heals, they feel better, and they can go back to work.
But it could be worse. They could spend years in chronic pain, or even be permanently disabled, unable to do some of the basic functions that people want to do, like walk, pick up a coffee mug, or even stand up straight.
And during the pandemic, the focus on your associates’ health and safety is even more important. Not only are people already at potential risk of getting hurt, but now they’re at risk of catching a disease that could kill them, leave them with long-lasting effects, or if they’re fortunate, only make them ill for a short while.
That’s why companies need to be even more focused on health and safety. Double down on safety requirements and safety training. Stand firm on requiring masks while people are on company property. And, if you think it’s warranted and you’re ready for the fight, require vaccinations for everyone who does not have a medical condition.
There’s also an increased risk of lawsuits from people who get sick on the job. If you require workers to come back when many people are still trying to stay home and avoid going out in public, you’re opening yourself up to lawsuits if you don’t take (and require) the necessary precautions to keep them safe.
That means requiring masks while people are working indoors. It means requiring social distancing in public settings, like working on an assembly line together. It may mean improving ventilation and air exchange in cafeterias and break areas, as well as in the factory.
Plus, there’s already a shortage of workers for a lot of jobs. Many of them who are still receiving unemployment from the government are content to stay at home because they’re making as much, if not more, than what they were making on the job.
While this shouldn’t be an issue for semi-skilled and high-tech labor (they make 3 – 5 times the unemployment rate), there’s still a worker shortage because of the pandemic. This may mean you need to recruit unskilled labor and train them heavily in skilled labor positions.
(Which means safety training becomes even more important since you have a lot of new employees on the floor.)
And finally, if your operation is large enough to support it, consider getting a nurse for your factory. This way, if anyone gets injured on the job, they can report immediately to the nurse’s office to get examined. Someone who injures their hand or arm can be treated immediately, without needing to visit the emergency clinic or the hospital ER. Those can be a lot more pricey — plus they create wild variations in your company’s healthcare costs — than having a nurse on staff. You can also work with outsourcing services that will place the nurse for you. This way, you can turn your healthcare costs into a static line item, not a randomly changing total that throws off your budget.
I’ve talked about the importance of safety before, and this year, as COVID continues to spread and surge, and there’s already a big worker shortage, it’s important that you keep your current workers healthy and safe. Not only for their own sake and that of their family, but to protect the company from the threat of lawsuits, lost productivity, and a bad reputation in the marketplace.
I’ve been a manufacturing executive, as well as a sales and marketing professional, for a few decades. Now I help companies turn around their own business, including pivoting within their industry. If you would like more information, please visit my website and connect with me on Twitter, Facebook, or LinkedIn.
Photo credit: Trapezemike (Pixabay, Creative Commons 0)