- February 17, 2021
- Posted by: David Marshall
- Category: Manufacturing
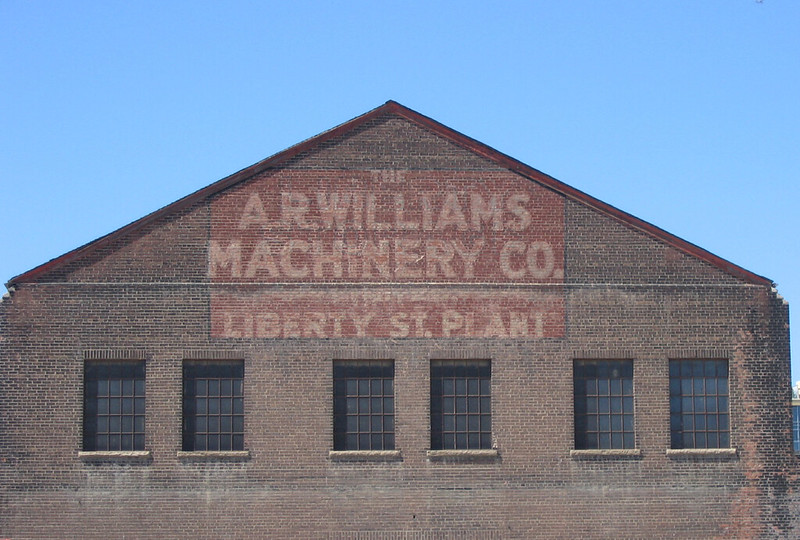
Over the last several years — decades, in fact — certain aspects of manufacturing have stayed the same. I could say the attitudes about change and disruption, but that would be a bit mean. And also untrue.
If you’ve paid attention to the automotive manufacturing industry, you already know the massive changes they’ve gone through since the 1970s: the disruption of the Japanese carmakers, the migration of the Japanese method of making cars, and now the cooperation between Japanese and American car manufacturers, as well as Japanese auto plants here in the U.S.
Technology has changed and improved in manufacturing as well. We’ve gone from hydraulic presses and labor-intensive processes that often resulted in injuries to Manufacturing 4.0: digital manufacturing, additive manufacturing, automation, and safety features that almost completely eliminate the risk of injury.
The one challenge that has remained absolutely consistent since the beginning of the first Industrial Revolution in my home country of Britain in 1760 is people.
Whether it’s in the C-suite or whether it’s on the floor with the lowest person on the org chart, people are always the same. And one of the big issues we’re seeing — just as we have seen over the last 261 years — is that people want to be treated with dignity.
They want to be valued, they want to be heard, they want to be paid fairly, and most of all, they want to be treated fairly.
In short, dignity.
That seems rather obvious today, but 100 years ago, when unions were being formed, factory owners seemed to take pleasure in mistreating their associates. They placed them in unsafe working conditions for very little pay.
Thankfully this has all changed for the better, but there are still companies that struggle with basic decency and treating their associates with dignity.
Of course, it’s happening now too in the software startup industry and the gaming industry, where the lessons of manufacturing unions seem to have been lost, but those companies tend not to last as that kind of management is not necessarily stable. You have to have leadership somewhere who’s willing to do the right thing.
The Manufacturing Skills Gap Is Another People Issue
The other people issue manufacturers are facing is the general skills gap.
According to the Predictive Index:
The country has an aging workforce consisting mainly of baby boomers. As such, the manufacturing sector desperately needs skilled, younger workers. (Approximately 22% of existing skilled manufacturing workers will be retiring by the end of 2025.)
Unfortunately, there aren’t currently enough workers to fill these roles. According to the Manufacturing Institute, there could be as many as two million unfilled manufacturing jobs by 2025.
This means manufacturers need to figure out how to close that skills gap locally, and possibly on their own. Don’t wait for people to show up or for your local trade school or community college to start pumping out new graduates to send your way.
You’ll need to partner with those schools in order to create those graduates, and may even want to help create the curriculum that will create the graduates that enter your company. Maybe even offer scholarships for anyone who wants to go into that field.
There’s a trucking school in Indianapolis that provides free driving education for all eligible students in one of the best truck driving schools in the nation? Why? Because the school is actually a recruiter for some of the largest transportation lines in the country, and they decided it was easier to just train new drivers than it was to track down existing ones.
You can also provide the upskilling training for existing employees to move up and fill those roles that will be emptying out in your plants. While automating a lot of your equipment and modernizing your production will help cut down on the number of people you’ll need for your operation, you’ll still need people who know how to operate the modern machines.
Just remember, as you bring in these new employees, dignity needs to be the watchword. Keep your employees satisfied, and they’ll remain loyal and spend years helping your enterprise achieve its fullest potential.
I’ve been a manufacturing executive, as well as a sales and marketing professional, for a few decades. Now I help companies turn around their own business, including pivoting within their industry. If you would like more information, please visit my website and connect with me on Twitter, Facebook, or LinkedIn.
Photo credit: Andrea Williams (Flickr, Creative Commons 2.0)