- February 10, 2021
- Posted by: David Marshall
- Category: Manufacturing, Safety
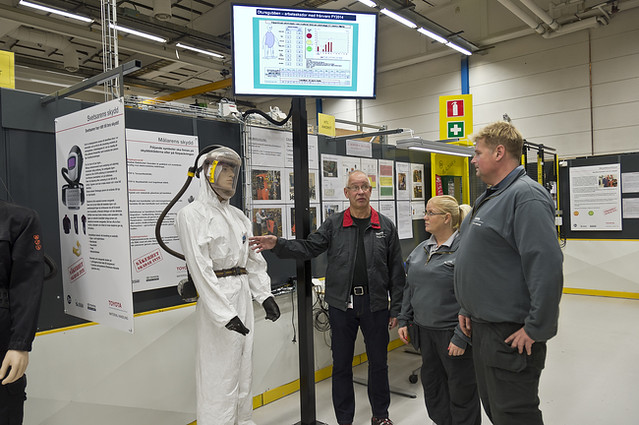
Ongoing safety training is critical in any manufacturing operation. It’s not just a one-and-done, set it and forget it type of operation.
Safety training is absolutely essential because your first priority in your business is human life. You absolutely, positively have to protect that above everything else; there are no two ways about it. Protecting the human condition and ensure the safety of all your employees is unparalleled. There’s no compromise and no room for “a little” collateral damage.
You’ve no doubt heard the expression that everybody makes a mistake, or seen those “Pobody’s nerfect” t-shirts. But there are some cases where that’s just not acceptable — 99.9% isn’t good enough. You don’t want a doctor that doesn’t drop 99.9% of the hearts she transplants. You don’t want 99.9% of airplanes to avoid flying into mountains.
Your safety goal should be 100% injury-free 100% of the time.
How often should you have safety training?
Honestly, you should conduct daily safety training in your operation. That’s a realistic expectation. Before the start of each manufacturing shift, you should have a safety meeting. Everybody should be reminded about their PPE, regular safety procedures (especially the new ones), and associates should have a chance to speak up about any issues with their equipment or policies.
I know a vegetation management/utility tree trimming service that does daily training briefings every single day, and they also touch on weekly units, addressing 52 different units throughout the year, such as chainsaw safety, lift buckets, PPE, and even dealing with wildlife. Once the year is up, they revisit the same topics.
In your manufacturing operation, everyone should also do an equipment check as soon as they reach their workstation, and anything that is not absolutely 100% operational should be shut down immediately and not touched until the issue has been totally resolved. The same is true in the tree trimming organization: they won’t operate a machine or use a safety harness if it shows signs of wear or fraying.
What about more complex safety training with videos and seminars?
Actually, this is less a function of safety training and more of a function of operational training. Safety training should be daily, but this operational training should just be ongoing, just not every day. It’s hard to specify any regularity on it, other than if there is any change in the operation, then everyone should be trained accordingly.
Also, it should be held on a regular basis to ensure that all new employees have seen the training.
You can use training management software to keep track of when people have participated in the training, including sharing safety training content via videos, testing participants on their knowledge, and keeping track of attendance and viewings via the software. This way, you can see at a glance if someone still needs to take their training or if they’re in danger of missing a deadline.
A tale of two airplanes: A metaphor for safety training
Recently, a 777 flight was flying from Denver to Hawaii. Shortly after takeoff, an engine exploded. The engine cowl fell down on a number of buildings, but thankfully no one was hurt. Initial reports show that the fan blades had metal fatigue, and as one fan blade broke away, it created the explosion.
You might mark it up to an aberration, a one-in-a-million chance. Except it happened a day earlier in The Netherlands, when a smaller version of the same Pratt & Whitney engine exploded on a 747 cargo plane.
Whether you’re a corrosion engineer or a metallurgist, you deal with metal fatigue all the time. You know that metal has a certain lifespan and after so many hours, it has to be inspected for fatigue and wear. But it looks like in both cases, the inspectors and engineers allowed their safety inspections to go so far to the edge of the envelope that this was the outcome.
Is this the sign of a bigger pattern or is it just a coincidence? For one thing, Pratt & Whitney will have some hard questions to answer. But the bigger question to answer is why did two separate airlines’ own engineers and inspectors let the problems become problems in the first place?
To me, this is a complacency issue on the operators’ part. They got so complacent that they relaxed their standards and let things slip through the cracks that shouldn’t have. The result was two engines blew up when they should have been repaired and maintained weeks and months prior.
Let’s apply this lax standard to safety training: What would happen if you only held weekly safety training? What would happen if you only trained your staff on important issues once a month?
Instead of daily and weekly training on chainsaw safety or dealing with wildlife, the tree service only trained employees one time when they first started? After a few years go by, that knowledge is no longer fresh and the associates will probably have forgotten most of it, which puts them at risk of snake bites and chainsaw injuries.
In this same way, the two airlines waited too long, got too complacent, and let things happen that shouldn’t have. The result is they got bit when they could have prevented these accidents. they’re only lucky that no one was injured and that all the property damage was minor and easily repairable.
Practice daily safety briefings and ongoing safety and operational training. Protecting your associates’ life, health, and well-being is your primary mission, even more than your profits and productivity.
I’ve been a manufacturing executive, as well as a sales and marketing professional, for a few decades. Now I help companies turn around their own business, including pivoting within their industry. If you would like more information, please visit my website and connect with me on Twitter, Facebook, or LinkedIn.
Photo credit: Toyota Material Handling (Flickr, Creative Commons 2.0)