- September 6, 2017
- Posted by: David Marshall
- Category: Business, Management, Manufacturing, Safety
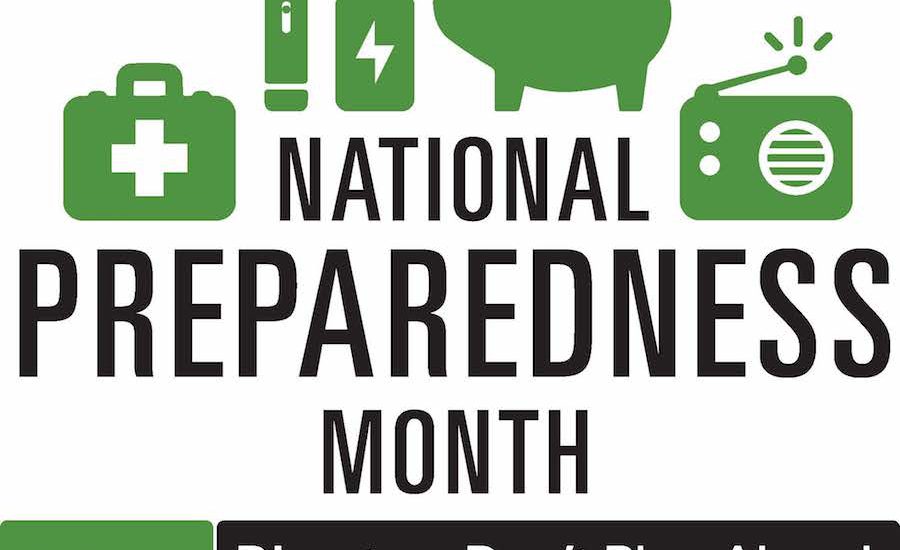
With Hurricane Harvey passing just a couple hours southeast of me, and Hurricane Irma hitting Florida, I have been wondering what businesses in the affected area have done to protect their data and information from disaster.
I’ve heard stories of businesses that have had to shut down because they lost their financial and client data to a flood or fire. They didn’t have a detailed disaster plan, let alone off-site backups of their most important data, and when it was gone, it meant they had no records of what they had sold, how much they were owed, or even who their customers were. All that was left to do was send everyone home and shut the doors.
This is something I have recommended to other businesses as well — build your recovery plan, and update it regularly. Be sure to update it to include all new capital projects that have gone into place since the last review.
It’s also important to make sure that someone (or some two) are in charge of the playbook, because someone has to know what’s going on while everyone else is running around like a chicken without a head. Someone has to know who to contact to have things done.
For example, once when I was in Dubai, we had a major fire in the post-cure oven, which is about the size of a railroad car. I had to cut my trip short and head home, but I also had my staff start contacting people to come in and start rebuilding and renovating even as the fire department was still wrapping up. I had people in my company who I could trust and rely on to carry out our recovery plan. You need those people too.
You also want to make sure you have your data and financial backups both onsite and offsite. We had a complete enterprise system backup with offsite equipment, and that was backed up on a daily basis. That way, if there was ever a disaster in Texas, we had a backup system in Michigan or Pennsylvania that would kick in and people could actually continue to work, so long as they had the ability to communicate and work from their homes. Plus all the data was current, so they didn’t have to deal with any gaps in information.
We also kept close track of our inventory with a warehouse management system and made sure we kept very good records of maintenance and the original documentation on all our equipment. We kept that in a secure database, along with our daily backups. At the very least, it would give us a starting point if something ever went wrong and we had to make insurance claims. Without that list, we would have had a problem since we wouldn’t be able to prove what kind of equipment we had, the age, or the condition and value.
Evacuation plans for tornadoes and fires were rehearsed a minimum of twice a year. And at least once a year, we held CPR training and fire control drills that were actually supervised by people from the fire department. They actually came in and instructed some of our people how to use fire extinguishers and let them practice with the equipment.
Another reason to rehearse your evacuation plans twice a year is that you need to ensure that your emergency lighting system is operable. If it isn’t, and you have a very large facility where everything goes black, you’re in for some trouble. Imagine many dozens, if not a few hundred, people trying to reach an unseen exit for a hundred yards or so. So during our evacuations, we checked all the lighting and replaced or repaired anything that might be broken.
Finally, while not strictly a large-scale disaster (except for the person involved), we also planned and trained for medical emergencies in case any individual got sick or injured. Certain people were trained in CPR and First Aid, and they were designated as first responders. We even asked them to wear a red shirt as part of their normal work attire so they could be easily identified at any moment.
If someone felt faint in the organization, the first responder would be there to make a very quick assessment of what was going on. They would take the person’s blood pressure and vitals to ensure that if they needed an ambulance, one was called. Or they could take someone to the hospital if the need arose. But we wanted to make sure we had people who could respond while any medical care was in transit, thus saving several precious minutes.
Safety has always been paramount for me — it’s the first of my four non-negotiables of management — and I stressed it every day at Robroy. And part of safety is having a disaster plan to follow in case things go wrong. If your company does not have one, create one immediately, and then start practicing the plan to make sure you’ve covered as much as you can.
I’ve been a manufacturing executive, as well as a sales and marketing professional, for a few decades. Now I help companies turn around their own business, and can help them create a disaster plan. If you would like more information, please visit my website and connect with me on Twitter or LinkedIn.
Photo credit: Defense Logistics Agency (DLA.mil, public domain)