- April 12, 2017
- Posted by: David Marshall
- Category: Management, Productivity
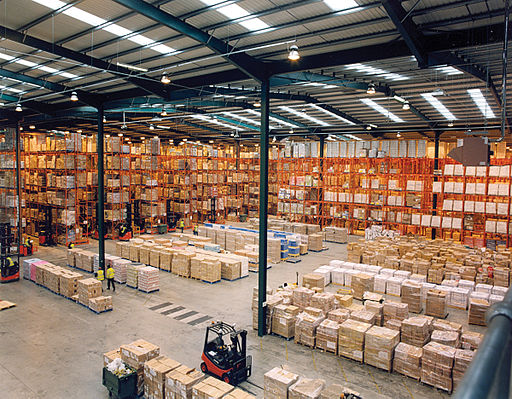
It’s an inventory cage match! Justin Case versus Justin Time
Can you imagine running a factory or business where it takes you 10 days just to do a basic count on your inventory? One of the problems is you might count something on Day 1 only to have to recount it because it’s been used up and replaced by Day 8.
This was the issue we faced when I started at Robroy Industries. We didn’t have a formal process in place, and we even had the problem that a lot of our incoming materials were stored on the floor in a large area near the receiving dock, and none of it was organized.
We had six people working round the clock whose sole job was to track down inventory in the big mess we had scattered around the floor. If you needed something, they would spend upwards of half a day looking for it. It also meant that inventory counts took longer as the counters had to chase down each item.
So I created a new goal for all of us. We would complete an entire inventory count of the entire plant within 24 hours. No more 10 day nonsense. Even two days was one too many.
Of course, the best way to do this is to invest in a warehouse management system (WMS). It’s an easy way to measure your entire inventory system. Everything that comes in is scanned via a bar code and is entered into the inventory system. The same thing happens when you take materials out of the system, or enter finished products back into the system.
Except we were nowhere close to being able to use a WMS. I believe they only let you continue with bad habits faster, and we had plenty of those, so we had to create some good habits first.
Second, we invested in a racking system to get all that incoming inventory off the floor and arranged into easy-to-find categories. By grouping similar products together and creating a more efficient search and retrieval system, we made things easier to find.
Finally, I required that we would take a wall-to-wall inventory count every 30 days until we could do it in one day, and we could also average a 95% accuracy by line item, not overall dollars. That meant we were counting everything by hand, not using bar codes or other technology. The result was that we changed the behaviors that would support a WMS.
How Did The Racking System Help
First of all, the racking system itself was nothing special. It’s the kind of shelf-and-rack system you see in a warehouse or a Lowe’s or Home Depot. But it was a real life saver in terms of our organizational efforts.
Without it, everything was laid out on the floor, where people could trip on it or the inventory would get damaged. We even had different clusters of the same part in different spots around the “inventory swamp,” so we could never be sure of how much we had.
But with the racking system, we were able to group items together in ways that made more sense. Not only were we able to assemble identical parts into a single area, we were able to combine similar items in close proximity.
We were also able to keep our most frequently used parts grouped together in the most efficient locations. If something was rarely used, it went to the far end of the racks. If it was frequently used, it was near the front. That let our inventory people pick the parts quicker.
The Final Results
Our new racking system and inventory process did two things for us.
First, it made it possible for us to buy that WMS, which our associates were greatly pleased with, because it meant we no longer had to do inventory counts every 30 days. Our new WMS allowed us to measure our inventory every 24 hours through cycle counts and reconcile it to our perpetual inventory.
When materials came in, we scanned their barcodes, and they were automatically added to the system’s inventory count. When someone needed some parts for a work order, those materials were scanned and removed from the inventory count. We were then able to track and make sure the finished products matched up to the required inventory by measuring it against the standards for each part. That solved a lot of inventory problems right there.
Second and more importantly, our excess and obsolete inventory went way down. Our total inventory dropped by 50 percent, saving us over $4 million just in one operation, all because we had been buying items we thought we “might need” rather than being able to easily identify what we were out of and ordering more at the very time we needed it.
In other words, we stopped buying “just in case” and started buying “just in time.”
I’ve been a manufacturing executive, as well as a sales and marketing professional, for a few decades. Now I help companies turn around their own business. If you would like more information, please visit my website and connect with me on Twitter or LinkedIn.
Photo credit: Axisadman (Wikimedia Commons, Creative Commons 3.0)